Recognizing the Basics and Applications of Plastic Extrusion in Modern Production
In the world of modern production, the technique of plastic extrusion plays an instrumental function - plastic extrusion. This elaborate procedure, including the melting and shaping of plastic through specialized passes away, is leveraged throughout various industries for the development of varied products. From car components to consumer products product packaging, the applications are large, and the possibility for sustainability is just as excellent. Unraveling the basics of this procedure reveals truth adaptability and potential of plastic extrusion.
The Basics of Plastic Extrusion Refine
While it might show up facility, the fundamentals of the plastic extrusion process are based upon reasonably straightforward principles. It is a production procedure wherein plastic is melted and then formed right into a constant account through a die. The raw plastic product, frequently in the kind of pellets, is fed right into an extruder. Inside the extruder, the plastic goes through warm and pressure, causing it to melt. The molten plastic is after that compelled via a designed opening, referred to as a die, to create a long, constant item. The extruded item is cooled down and after that cut to the desired size. The plastic extrusion procedure is thoroughly utilized in various sectors because of its cost-effectiveness, adaptability, and effectiveness.
Various Sorts Of Plastic Extrusion Techniques
Structure upon the standard understanding of the plastic extrusion procedure, it is necessary to explore the numerous techniques included in this production technique. The two main methods are profile extrusion and sheet extrusion. In profile extrusion, plastic is thawed and formed right into a constant profile, usually utilized to develop pipelines, rods, rails, and window frameworks. In comparison, sheet extrusion creates big, level sheets of plastic, which are commonly additional processed right into products such as food packaging, shower drapes, and automobile components. Each technique calls for specialized machinery and accurate control over temperature level and pressure to make sure the plastic keeps its shape throughout air conditioning. Recognizing these strategies is key to utilizing plastic extrusion successfully in modern manufacturing.
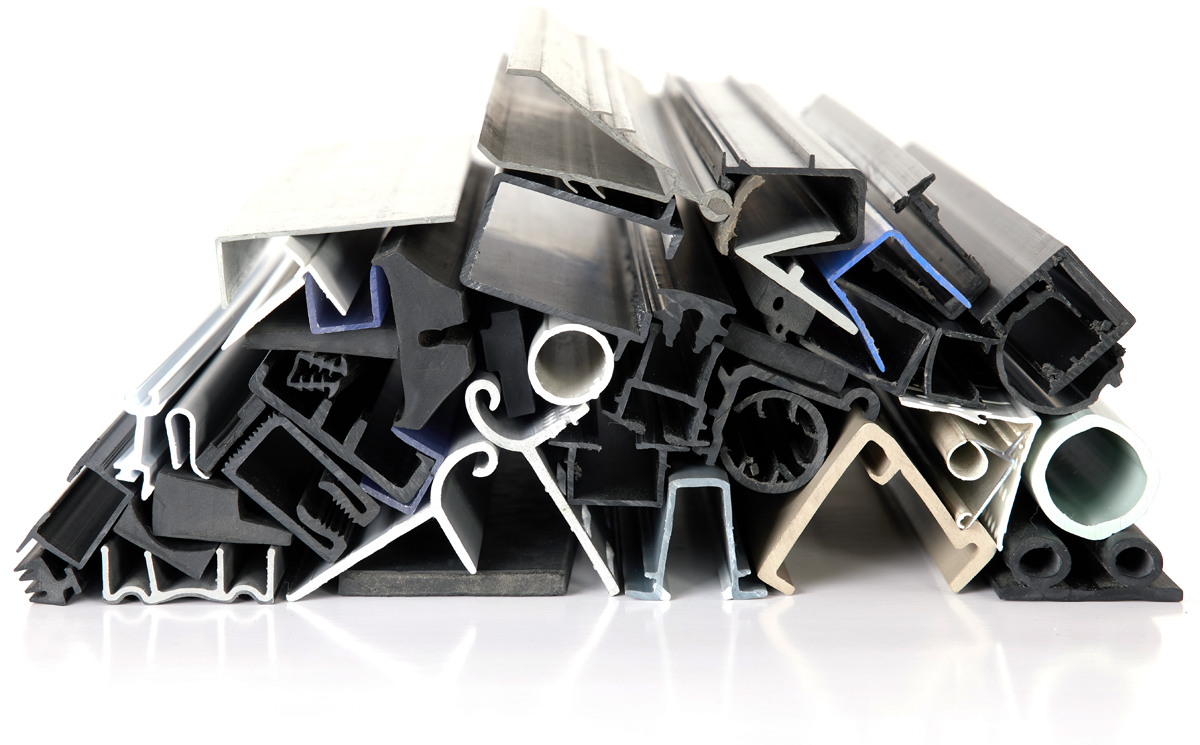
The Function of Plastic Extrusion in the Automotive Market
A frustrating bulk of parts in modern-day automobiles are items of the plastic extrusion why not try these out process. Plastic extrusion is largely made use of in the production of different auto parts such as bumpers, grills, door panels, and dashboard trim. Therefore, plastic extrusion plays a crucial duty in automobile manufacturing.
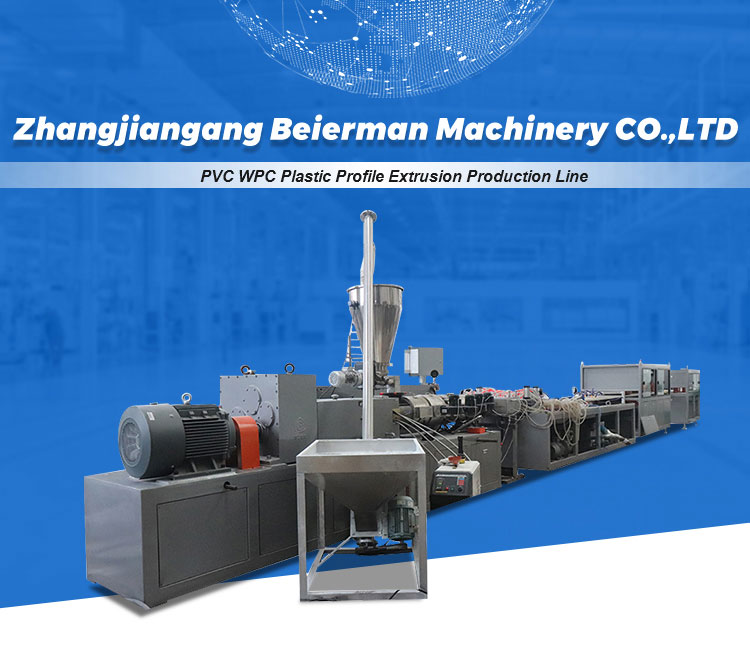
Applications of Plastic Extrusion in Consumer Goods Manufacturing
Past its significant impact on the automobile market, plastic extrusion proves just as reliable in the realm of durable goods producing. This procedure is he said crucial in creating a wide variety of items, from food product packaging to house home appliances, playthings, and even medical devices. The versatility of plastic extrusion allows manufacturers to design and create complicated sizes and shapes with high precision and performance. Due to the recyclability of lots of plastics, squeezed out elements can be recycled, decreasing waste and cost (plastic extrusion). The flexibility, adaptability, and cost-effectiveness of plastic extrusion make it a favored option for many durable goods makers, contributing significantly to the sector's development and technology. The ecological implications of this widespread use call for cautious consideration, a subject to be talked about better in the succeeding area.
Environmental Impact and Sustainability in Plastic Extrusion
The prevalent use plastic extrusion in manufacturing invites scrutiny of its environmental implications. As a procedure that regularly makes use of non-biodegradable products, the environmental impact can be significant. Power consumption, waste production, and carbon discharges are all issues. Nevertheless, sector improvements are increasing sustainability. Effective machinery decreases power use, while waste monitoring systems great post to read reuse scrap plastic, decreasing resources needs. In addition, the growth of biodegradable plastics supplies a much more eco pleasant alternative. In spite of these enhancements, better innovation is needed to mitigate the ecological footprint of plastic extrusion. As culture leans towards sustainability, makers have to adjust to remain sensible, stressing the relevance of continuous research study and advancement in this field.
Conclusion
Finally, plastic extrusion plays an essential function in modern manufacturing, especially in the auto and customer items markets. Its adaptability permits the production of a vast array of elements with high accuracy. Its possibility for recycling and growth of eco-friendly materials supplies an encouraging method towards sustainable techniques, consequently resolving ecological problems. Understanding the basics of this procedure is vital to enhancing its advantages and applications.

The plastic extrusion process is thoroughly used in numerous markets due to its efficiency, cost-effectiveness, and versatility.
Structure upon the basic understanding of the plastic extrusion process, it is essential to check out the different methods included in this manufacturing approach. plastic extrusion. In contrast, sheet extrusion develops large, level sheets of plastic, which are usually further processed into items such as food packaging, shower curtains, and vehicle components.A frustrating majority of components in contemporary vehicles are products of the plastic extrusion procedure